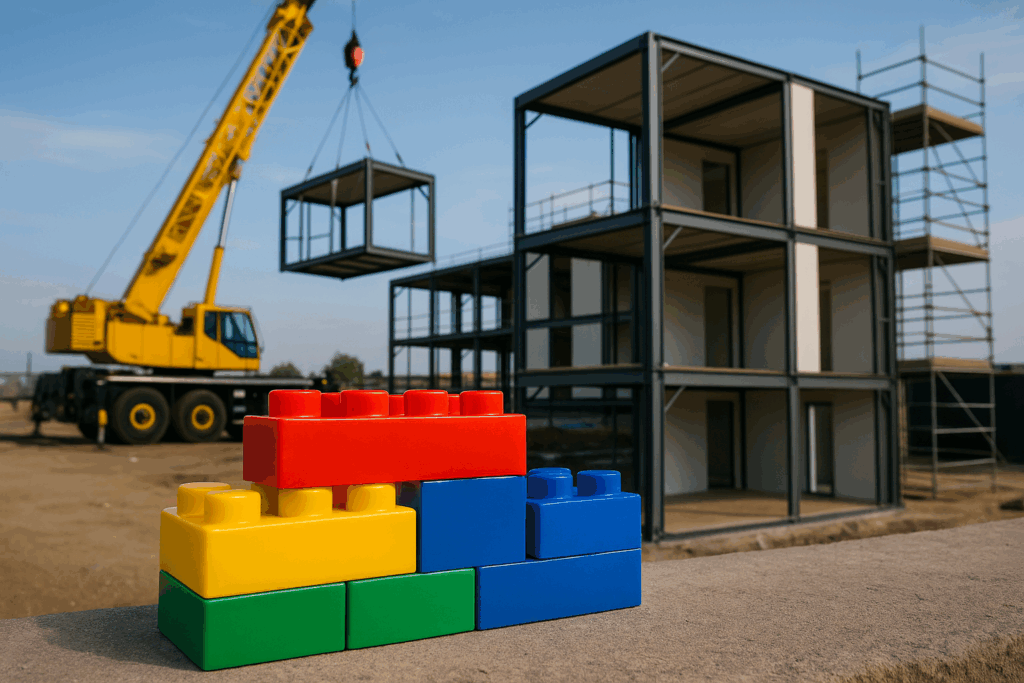
What if constructing a building was as easy as snapping together Lego bricks? Modular steel construction is turning that dream into reality. This blog explores how off-site fabricated steel modules – our grown-up Lego blocks – are revolutionising building speed, efficiency, and sustainability. Expect insights on the latest modular projects, benefits and challenges, and a pinch of humour about builders playing with blocks.
Building Blocks, But For Real
Walk onto a modern construction site using modular methods, and you might feel like you’ve wandered into a life-sized Lego set. Giant steel-framed modules – essentially fully fitted “blocks” of rooms – arrive on trucks, get hoisted into place, and click (or rather, bolt) together to form a building. This isn’t science fiction; it’s happening now and gaining momentum. Modular steel construction involves manufacturing large sections of a building (often whole rooms or sections of floors) in a factory, then assembling them on site like pieces of a puzzle. Each module comes complete with steel structure, floors, walls, and even interior finishes. Stack them up, connect the utilities, finish the façade, and voila – a building emerges in a fraction of the time of traditional construction.
Why the rise of this approach? In short, speed and efficiency. A controlled factory environment means you can build rain or shine, with no pauses for Britain’s famously unpredictable weather. Multiple modules are produced in parallel, so the on-site assembly is blazingly fast. One oft-cited extreme example is a Chinese company erecting a 10-storey apartment block in just 28 hours and 45 minutes using modular units – practically an overnight sensation. While that was a showcase stunt, it underlines the potential. Even in less extreme cases, modular projects routinely shave months off build programmes. Time is money in construction, so saving time saves plenty of money (and interest on development loans, which will make any finance director smile).
The Steel Backbone of Modules
Not all modular construction is steel – some use timber or concrete – but steel modules have unique advantages. A steel frame is both strong and slim, maximising usable space within each module. It also ensures precision: steel components are fabricated to millimetre tolerances with modern techniques, meaning your modules slot together accurately on site. Think of that satisfying click when two Lego pieces join – modular steel aims for that level of precision (minus the thumb pain you get from separating Lego plates!).
One of the trailblazers has been high-rise modular construction. The world’s tallest modular buildings, at least until recently, were two 44- and 38-storey residential towers in Croydon, South London, known as “Ten Degrees”. Built by Tide Construction, these towers (135m and 125m tall) were composed of 546 steel-framed modules stacked up. The entire project was delivered in just 39 months from the first sketch to handover – lightning speed for a pair of skyscrapers. Impressively, the precision factory process and efficient design resulted in a 40% reduction in embodied carbon compared to a traditional build of similar scale. In other words, modular can be greener: less waste (factory production optimises material use and recycling), and less idling of machinery on site. It’s inherently sustainable “due to its efficient use of materials, reduction of onsite waste, and lower energy consumption during the build”.
The steel modules in Croydon were fully outfitted – including internal fittings – before they left the factory. This highlights another benefit: parallel working. While modules were being craned into place on site, other modules were still being fitted out back at the factory. It’s the ultimate fast-track – akin to building with Lego while someone else paints the Lego bricks in another room.
Advantages: Why Go Modular?
Besides speed, modular steel construction offers a laundry list of benefits:
- Improved Quality Control: Factories don’t have to deal with mud, rain, and trades tripping over each other. Work is done at ergonomic heights with jigs and fixtures to ensure alignment. The result is often higher build quality and consistency. Think of it like the difference between a hand-made car and one from an automated production line – the factory product is more likely to have uniform welds and plumb walls.
- Safer Working Conditions: Fewer personnel working at height or in inclement weather. Assembly on site is quicker and simpler, reducing high-risk activities. (And no one is precariously perched on scaffolding trying to weld a beam 30 metres up in a gale – much of that work was done at ground level in the factory.)
- Less Disruption: Neighbours of modular construction sites often can’t believe how quickly the structure appears. Shorter construction time and fewer big material deliveries mean less noise, dust, and disruption around the site. For projects in busy city centres or near schools/hospitals, that’s a huge plus.
- Predictability: Since so much is pre-made, the project timeline is more predictable. There’s less risk of on-site delays due to weather or labour shortages. Similarly, costs can be more predictable – fewer surprises because the bulk of construction happens under controlled conditions. (No unexpected expense because a storm ruined your fresh concrete pour, for instance.)
However, let’s not kid ourselves that it’s all sunshine and roses (or bricks and bases). Modular construction does come with challenges.
Challenges: Not Quite Child’s Play
If modular is like Lego, it comes with the caveat that you must design the Lego pieces correctly from the start. One major challenge is the design and coordination upfront. Architects and engineers need to lock in the design early and with great detail. There’s less flexibility for last-minute changes, because a tweak in one module could affect fabrication of dozens of units. It requires a mindset shift to “design for manufacture and assembly (DfMA)” at the earliest stages. Traditional projects might tolerate a bit of design development during construction; modular projects demand decisions sooner. (In other words, no late “oops, let’s move that wall” moments unless you fancy retooling a factory line.)
Transport and lifting logistics also impose limits. Modules are big and heavy – usually limited by what can fit on a lorry and beneath overpasses. Typically, modules might be 3 to 4.5 metres wide and perhaps 8 to 12 metres long. Anything bigger becomes impractical to haul down the motorway. This means modular designs often must be broken into these chunk sizes, which can influence the apartment layouts or room sizes. Structural engineers also have to consider that each module has to withstand lifting forces (being hoisted by a crane at one or two points) in addition to final in-place loads. Steel modules are robust, but extra bracing or frame action might be needed during the pick-up.
Then there’s the matter of connections. When stacking modules, how they lock together structurally and transfer loads is crucial. Typically, steel connector plates or brackets are used at the corners, and workers bolt modules to each other and to the primary structure (like an internal core or podium). Getting a perfect fit on site requires precision in fabrication. If modules arrive even slightly out of tolerance, stacking could become a nightmare (“Houston, the blocks don’t fit!”). Thankfully, modern CNC fabrication and rigorous factory QA/QC make it feasible to achieve the needed precision. Still, assembly crews need good training – it’s a bit like a barn-raising but with steel boxes, and a mistake in aligning the first few could cascade through the structure.
Lastly, perceptions and planning approval can be hurdles. Some still (unfairly) associate modular with bland, cookie-cutter buildings or temporary site huts. The industry is rapidly overcoming this with high-profile attractive designs, but early on you might need to convince clients and planners that “modular” doesn’t equal “modest.” In fact, modular buildings can look indistinguishable from traditional ones once completed – the Croydon towers, for example, are clad in a stylish façade; no one strolling by thinks “looks like a bunch of shipping containers” (because they’re not!). Architects have plenty of freedom in façade treatment and massing; the module grid is just a starting framework.
Modular Marvels: Recent Projects
We mentioned Croydon’s record-setting towers, but modular steel is popping up in many sectors. Hotels are a natural fit – identical room modules make factory repetition efficient. Hilton and Marriott have embraced modular construction for some new hotels, cutting construction time significantly. For instance, a Hampton by Hilton in Bristol was assembled floor by floor from prefab modules, speeding up delivery in a tight urban site.
Hospitals and student accommodations also use modular units, especially for extensions or rapid builds. During the COVID-19 pandemic, modular construction provided emergency medical facilities in record time, leveraging the ability to fabricate units for wards and labs off-site while site prep was still ongoing.
Even the residential mid-rise market is seeing modular make waves beyond the UK. In the U.S., a 32-storey tower in New York (461 Dean) opened a few years ago as one of the tallest modular buildings in America, proving you can go high with this method (though not without learning pains and delays in that case—highlighting that expertise is still growing).
On the quirkier side, modular doesn’t have to mean boring boxes. Designers are experimenting with module configuration, offsetting modules to create dynamic forms and even leaving some modules partially cantilevered for architectural effect. It’s a bit like when advanced Lego builders create something that doesn’t look like it was made of Lego at first glance.
The Future: Plug-and-Play Buildings?
As technology and familiarity improve, modular steel construction could become a staple for a larger portion of new builds. Think of a future where buildings are assembled from a kit-of-parts produced in local module factories – perhaps even with robotic welding and automation to further speed production. We might also see more hybrid systems, where the core and lower floors of a building are done in concrete or on-site steel, but everything above in repeated modules. This can blend the benefits (a very tall building might keep a traditional core for stiffness but use modules for the hotel or apartment floors above).
Sustainability will also drive modular adoption. The ability to disassemble buildings at end of life and potentially re-use modules is an exciting concept. Imagine treating modules as circular economy products – today it’s a hotel room, in 30 years that same module is refurbished and becomes a student dorm (just like repurposing Lego pieces into a new creation). This is easier said than done (planning and building codes aren’t quite there yet to swap building parts like batteries), but the idea is on the horizon.
In conclusion, modular steel construction is no longer an odd experiment; it’s an increasingly mainstream method with proven successes. For construction professionals, it means adjusting workflows: more upfront planning, closer collaboration with manufacturers, and a shift for site teams from “building” to “assembling.” For clients, it means faster returns on investment and potentially higher quality. And for our industry’s future recruits raised on Lego and Minecraft – you’re in luck. You truly can keep playing with blocks when you grow up, only now the blocks are a bit bigger (and you’ll need a hard hat).
As one site manager quipped, the modular approach is “so satisfying, it’s like finishing a Lego set – but one that people will live or work in.” With results like these, who wouldn’t be “building like Lego”?